ADVICE – Using a Torque Wrench
If you’re improving your maintenance skills with your 4x4, you need to improve your tools as well. That’s where a torque wrench comes in.
To the novice, a torque wrench may seem an excessive, maybe even unnecessary, addition to the toolkit. But if you’ve ever broken a bolt when tightening it, or are rebuilding an engine that requires specific bolt tension, you’ll appreciate the value of a torque wrench. For a few hundred dollars, it’s an investment that can save you a LOT of extra cost down the track.
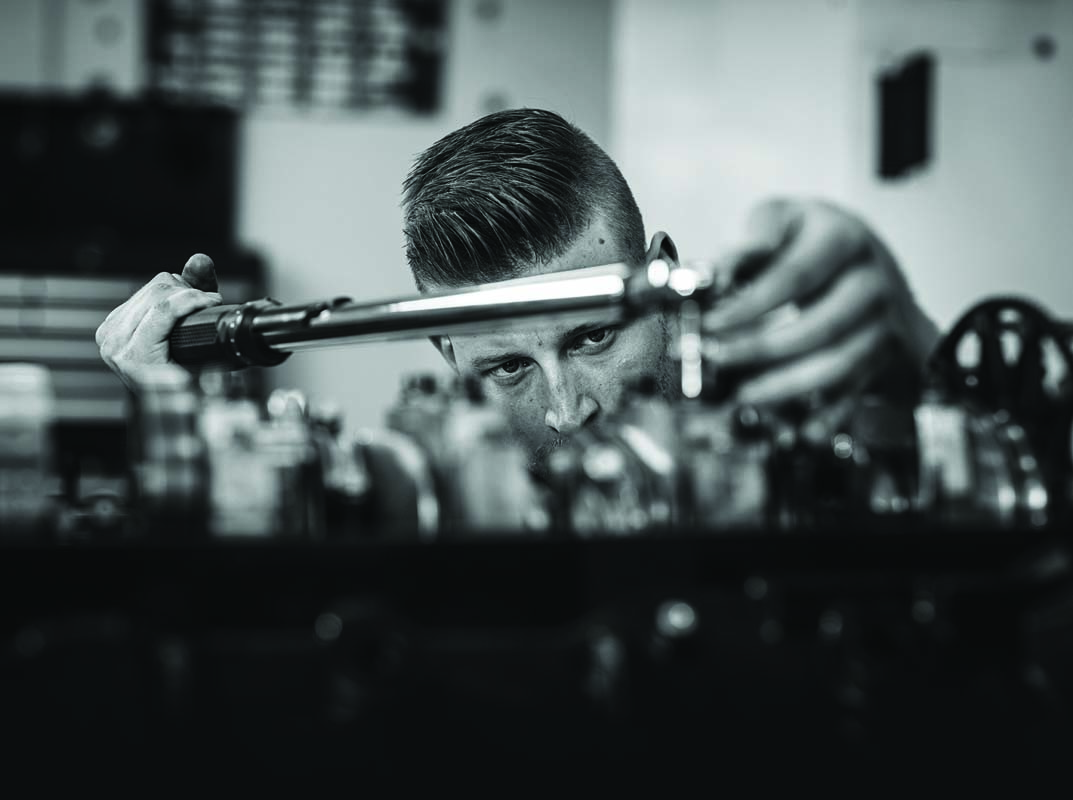
If you Don’t Know, Don’t Go.
If you’re not fully confident in using a torque wrench, don’t use one – it’s as simple as that.
Correct use of a torque wrench requires some knowledge of not only the tool itself, but what you’re using it on. If you don’t know the recommended torque settings for whatever it is that needs tightening to a specific tension on your 4x4, then a torque wrench is of little use.
Torque settings can be found in your vehicle’s relevant service and repair manual. If you don’t have a manual, you can search online, but treat online info with caution – try numerous sources for an average to get an idea of the “right” setting.
Again, if you’re not sure, leave any work that requires a torque wrench to a professional mechanic.

The Right Choice
The most common types of torque wrench – 1/2-inch, 3/8-inch and 1/4-inch drive – suit most existing socket sizes for four-wheel drive applications and offer a range of torque settings, like 5 to 25Nm or 70 to 350Nm, for example.
Understand what sort of bolts and nuts you’re most likely to be torquing down, as the range of tension needed will determine which wrench (or wrenches) you’ll need to buy.
Some torque wrenches have a digital display and offer more finite adjustment, while most have a reversible ratchet head, meaning they can tighten left- and right-hand thread bolts.
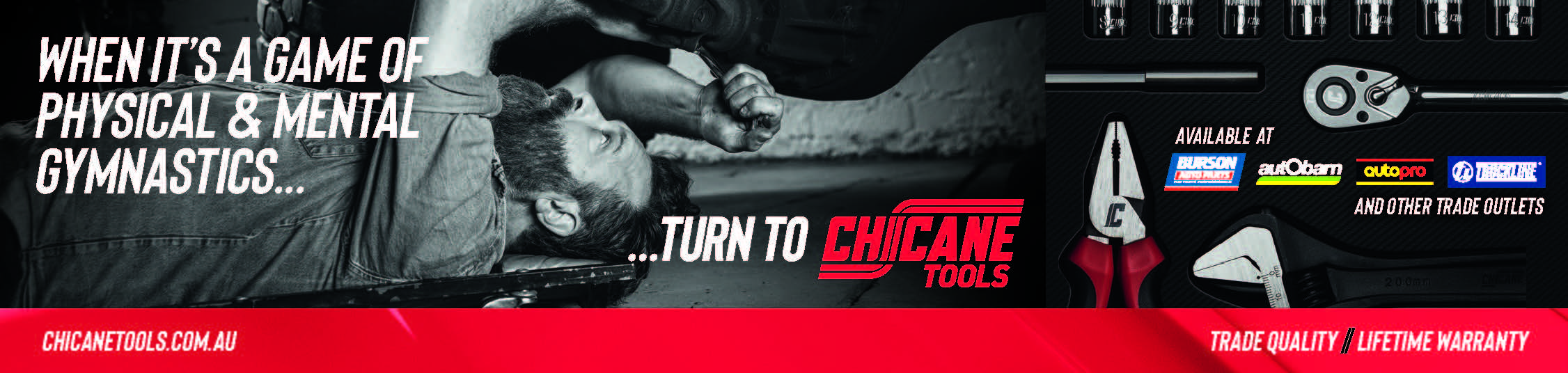
Loosen, Set, Tighten . . . and Tighten.
Once you know the torque settings required and are familiar with the torque wrench, using it is pretty simple. Start by loosening the collar or locknut at the base of the wrench, which allows the rotating handle to be dialled up to the required torque setting. These settings are marked in increments on the shaft - usually Newton Metres (Nm) and/or Kilogram Force (kgf-m) on one side and foot-pounds (ft-lb) on the other. Further markings on the handle allow for more finite adjustment, down to single and percentage Nm units in some cases.
Once the required torque setting is in place, tighten the collar/locknut - this holds the selected setting in place. Then it’s just a matter of attaching the relevant socket to the wrench’s ratcheting head and tightening the nut or bolt.
Most torque wrenches will give an audible ‘click’ from the ratchet head when the desired torque has been achieved. When you hear that, the pre-set torque for the nut or bolt has been achieved and the job’s done.

Care and Maintenance
Torque wrenches are precision instruments, so don’t use them for general nut and bolt tightening or as a breaker bar. It’s unlikely you’ll need a torque wrench when out bush, so leave it at home in the security of your garage.
As they’re precision instruments, torque wrenches do require care. Dropping the wrench or getting it wet and muddy can damage its internal spring, leading to incorrect calibration.
That spring is under tension, too, so after use, dial the wrench down to its lowest setting, as this places the least strain on the spring.
If the wrench comes with its own carry case, use that for storage, rather than have it loose in a toolbox.
After a prolonged period in storage, a torque wrench may need recalibrating, which should be left to a tool professional. Even if used regularly, annual checking of the calibration by a professional is recommended to ensure the wrench remains accurate.